Industrial manufacturing for the digital age
Industrial manufacturing is undergoing a rapid transformation and the pandemic accelerated the pace of change. Digital technologies and changing customer demands are revolutionising the manufacturing landscape and how value is created, dramatically increasing the overall level of uncertainty.
Still, there are many opportunities to drive growth. Industrial manufacturing 4.0 — or the manufacturing for the digital age — is based on digital technology and novel methods such as big data and analytics, smart interconnected devices and cloud computing, advanced robotics and automated machines as well as additive manufacturing (3D printing) and advanced materials.
Big data analytics
Modern manufacturing is a data-rich environment that supports the collection, transmission, sharing, and information analysis across the organisation to produce invaluable intelligence.
The global big data analytics in the manufacturing industry was valued at USD 904.65 million in 2019 and is expected to reach USD 4.55 billion by 2025, growing at a CAGR of 30.9% from 2020 to 2025.
Like most organisations, industrial manufacturers are creating a growing digital footprint and have access to operational and business data from their processes, assets and workflows. They can leverage this vast amount of data about their inventories, products, people, and finances to gain a competitive advantage, control costs, optimise the use of resources and manage sustainability efforts amid evolving regulations. Big data analytics enable manufacturers to optimise manufacturing and field operations and respond to key business needs by integrating the data from and into the products themselves. Big data fuels other novel technologies such as the Internet of Things, robotics and automation and AI. Intel cites automation and the effective use of data as core elements of its competitive strategy.
Industrial Internet of Things
Internet of Things refers to the network of interconnected devices that communicate via embedded sensors and wireless networks. It is revolutionising the businesses across the board.
Data-gathering and analytics capabilities enabled by the interconnected devices offer a new source of value across the whole of the supply chain and manufacturing processes, opening new possibilities never seen before.
IoT allows operational technology and information technology to join forces to transform manufacturing and empower organisations to create new ways to optimise operations and engage with customers.
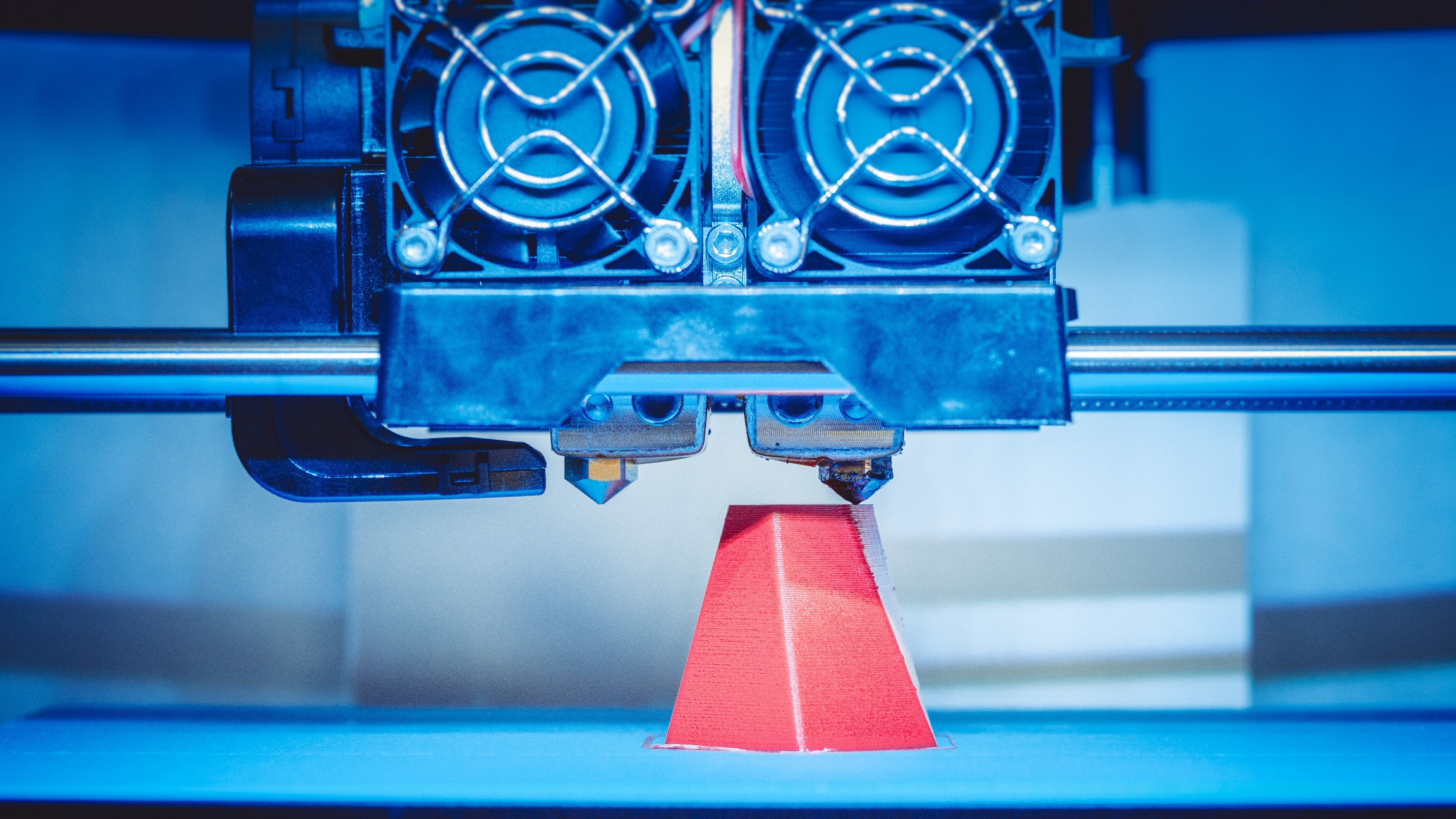
IIoT or a network of interconnected devices, products and people applied in industrial settings leverage the massive amount of data produced in organisations every day to extract deep insights they can use to optimise business and manufacturing processes by streamlining operations, making better, data-driven business decisions, and using predictive analytics to see the changes in customer behaviours as they emerge.
The impact on the bottom line is palpable. It is estimated that IIoT will increase manufacturing productivity by 10-25%, unlocking up to $1.8 trillion in global economic value by 2025. At the same time, IoT applications in manufacturing are expected to generate $1.2 to $3.7 trillion of total economic value annually by 2025.
IoT devices and Big Data-powered predictive analytics applied in all areas across the board, including supply chain management, operating efficiency and predictive maintenance, enable manufacturers to reduce overhead, save resources, increase profits, and optimise operational efficiencies. According to the American Society for Quality, 82% of manufacturers which digitised their businesses increased operational efficiency and improved product quality with 49% fewer product defects.
Connected products enable manufacturers to provide continuous monitoring and offer data-driven predictive maintenance services to their customers, detecting issues before they escalate into problems. IoT is a powerful novel technology that enables manufacturers to scale easily, go to market faster and expand their offering from a holistic platform.
Robotics
The use of robotics is increasing across the value chain – from production to warehousing, distribution and customer management – helping manufacturers optimise productivity, reduce defects, and cost-effectively streamline supply chains. As one of the IoT devices, capable of adjusting to changing production and logistics environments, robots can receive signals from interconnected equipment and send them to digital platforms where they are collected and analysed as a large number of datapoints carrying invaluable insights.
Additive manufacturing (3D printing) and distributed production
Additive manufacturing, also called 3D printing, refers to digital technologies that allow the creation of a three-dimensional physical object from a digital model.
It is called additive as materials are added layer by layer instead of subtracted like in a conventional manufacturing process. Because materials are only consumed (or added) where needed, considerably less material is wasted.
According to 3D Printing Industry research, additive manufacturing revenues have been growing rapidly at the annual rate of 27% over the past three decades and is expected to reach $44.39 Billion by 2025. The explosive growth is driven largely by benefits such as the reduction in manufacturing errors, development cost and time, and the capacity to build customized products.
3D printing enables manufacturers to transform the supply channel by leveraging digital warehouses and the so-called distributed manufacturing on-demand. This novel approach involves a decentralized network of 3D printers located at or near the point of use that replace traditional centralised manufacturing facilities to better meet customers’ needs and deliver goods when and where they are needed.
By being close to the end-user, on-demand distributed production reduces inventory costs, lead time, and dependency on demand forecast as the production is flexible enough to respond to unpredictable customer demand at no additional logistics costs, such as transportation, customs and taxes.
The power of digital technology for the new era of manufacturing
Digital technology is powering a new industrial revolution, impacting all aspects of manufacturing, leading to radical improvements in speed, quality, productivity, and flexibility. At the same time, it is getting more and more affordable as robots and sensors are getting less expensive but also efficient and easier to use.
Advances in information technology bring rapid transformation to traditional manufacturing, changing the landscape and enabling manufacturers to achieve operational excellence and differentiate themselves in an increasingly competitive market. Unleashing the power of digital technology for manufacturing fit new era involves collaboration between people and machines. AI-enabled advanced data analytics results in machines taking increasing responsibility for decision-making in manufacturing and will require upskilling for the workforce to enable people to work alongside machines. For manufacturers that embrace digital transformation, the benefits are vast.
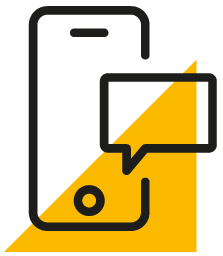
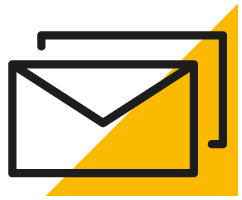